LCVP MK5B
Date: June 2017
Customer: Babcock International Group
Location: Devonport Royal Dockyard
Background
An LCVP MK5B required protecting from corrosion for a period of up to 5 years, whilst being stored outside (not on the water).
1) The Task
Babcock approached HITEK-nology Solutions Ltd (HSL) to provide a solution that would result in equipment being protected from corrosion, whilst at the same time allowing access to all parts of the craft for any maintenance etc.
2) Product Used
- VpCI 101
- VpCI 105 Emitters
- VpCI 137 Foam
- VpCI 322
- VpCI 415
- VpCI 705
- M529
- M640L
- MilCorr
- CorrShield 368 Aerosol
- CorrShield 369 Aerosol
- CorrLube Grease
3) The Solution
The LCVP was washed down with VpCI 415.
VpCI 705 was added to the fuel, M529 was added to the engine and gearbox oils, M640L was added to the coolant system, VpCI 322 was added to the hydraulic systems, the engines were then run up for approximately 20 minutes. The engines were then removed for storage else where.
All electric junction boxes were treated with VpCI 101 and 105 emitters.
All exposed bare metal was treated with CorShield 368, and any exposed metal that also required lubrication (e.g.) ramp rams were treated with CorShield 369.
The engine compartment, well space, wheel house and deck area were treated with VpCI 137 foam.
The LCVP was then wrapped in MilCorr which was then subsequently heat shrunk into place. A MilCorr zip door was then added so that access could be gained to all parts of the craft.
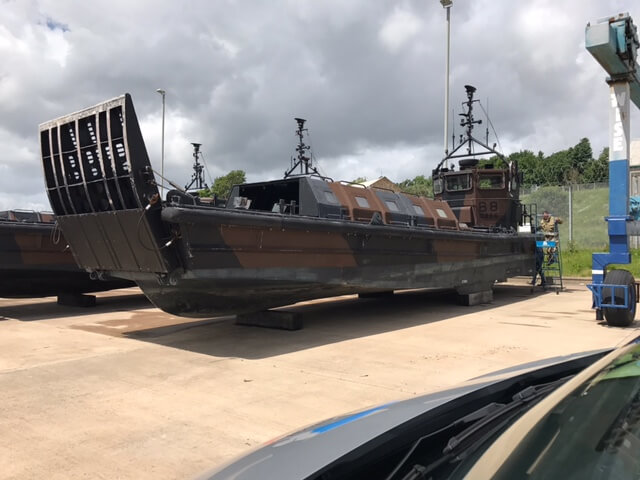
Before
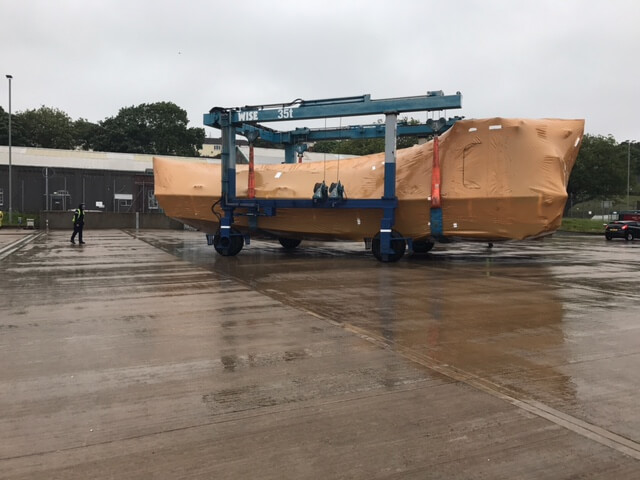